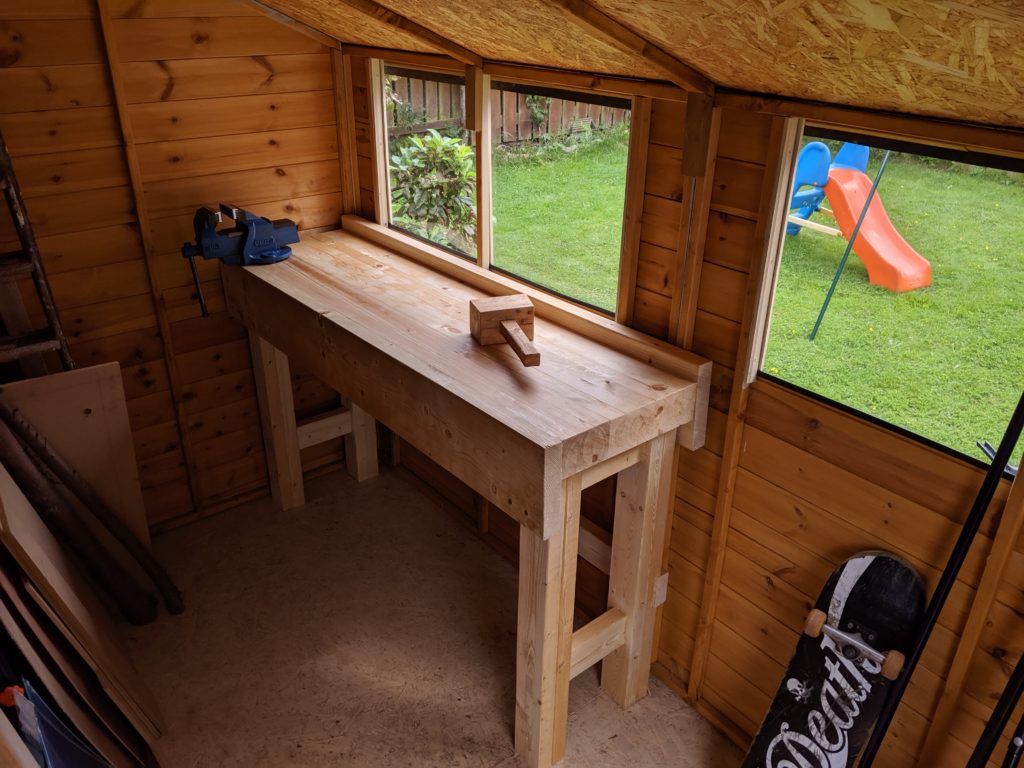
Suministros
Materiales:
Secoya (pino) 50mm x 100mm x 4,8m(estaba más cerca de 47mm x 94mm ahora que está seca) : Tres
Viguetas 47mm x255mm x 3.6m: Una
Viguetas 47mm x 100mm x3.6m: Tres
Cola de madera PVA
Clavijas de 10mm
Tornillos
Herramientas:
Tambien te recomiendo leer: Emprende con la resina epoxica y la madera creando mesas de rio . 5/5 ⭐⭐⭐⭐⭐
Sierra de corte:
Evolution 252 SMS UK Amazon link
Enlace Amazon Evolution US
Abrazaderas de faja
Abrazaderas en C
Liso
Escuadra
Sierra circular:
Evolution Rage-B UK Amazon link
Evolución Rage EE.UU. enlace de Amazon
Sierra de mano
Cincel
Mazo – Tengo un instructable de él aquí, hecho de trozos de corte de la encimera
Taladro
Brocas Forsner
Paso 1: Encimera
La encimera está hecha de pino laminado vestido 100mm x 50mm. Corté la madera a la longitud aproximada, quería que el banco fuera de 1,5m de largo y el stock venía en 50mm x 100mm x 4,8m así que corté cada una de las tres longitudes en tres piezas de aproximadamente 1,6m.
El pegado fue el más grande que he hecho y en realidad más fácil de lo que esperaba, puse las abrazaderas y añadí bastante PVA a un lado de cada longitud. Intenté mantener todo plano usando abrazaderas en C en algunas tablas en cada extremo.
Después de que estaba seco usé una llanura para aplanarlo, los palos de bobinado ayudan a comprobar si hay una torsión a lo largo de la longitud.
Paso 2: Patas
Se hizo un par de patas utilizando cuatro uniones de mortaja y espiga. Las viguetas de 47mm x100mm x 3,6m se cortaron en ocho longitudes de 860mm y se pegaron de dos en dos, también corté cuatro longitudes de 455mm para los travesaños.
Primero corté las mortajas para poder dimensionar las espigas al tamaño real del agujero que iba a cortar – mi objetivo era 25mmx50mm. Quité la mayor parte del material para la mortaja con una broca de forsner y luego utilicé un cincel para limpiarlas a escuadra.
Primero corté el lado más corto de la espiga para facilitar el lado más largo. Una vez cortada la espiga, la recorté a la medida correcta con un cincel.
Paso 3: Montaje
Corté la viga de 47mm x 225mm x 3,6m en dos tramos de ~1,6m, la misma longitud que la encimera. Corté 10mm de la parte superior del faldón delantero para que tuviera un borde cuadrado que se encontrara con el resto de la encimera. La parte trasera es 50mm más alta que la encimera para que no pueda golpear las herramientas y los lápices en la parte trasera.
Es probable que la encimera se encoja durante el primer año aproximadamente, lo que significa que tengo que tener cuidado con la forma de fijar las patas, ya que de lo contrario se desprenderá. Así que estoy usando clavijas y pegamento para fijar las patas al faldón delantero, hay un pequeño espacio entre la parte trasera de las patas y el tablero trasero y las patas se fijan a él con tornillos que pueden moverse a través del tablero trasero. De este modo, si la encimera se encoge, puedo apretar un poco los tornillos y todo estará bien.
Con las patas unidas a la encimera, añadí un refuerzo a la parte trasera usando un trozo de viga de 47mm x 100mm usando juntas de media vuelta, estas fueron aseguradas con tornillos mientras el pegamento se secaba – ¡estaba compitiendo con el tiempo para meterlo dentro antes de que lloviera y es un bulto para mover!
Paso 4: Vicio de Moxon
Con el banco montado y utilizado un poco, vi que un tornillo de banco estilo Moxon en el lado izquierdo sería un complemento útil.
El tornillo de banco Moxon o de doble tornillo fue descrito en Mechanick exercises por Joseph Moxon. No afirma haberlo inventado y lo menciona como uno de los métodos de sujeción/apriete estándar. En la década de 1800 se produjo un aumento del uso de barras/tuercas roscadas debido a la mayor precisión del proceso de corte del torno, pero las roscas de los tornillos existían desde antes del siglo III a.C. y los romanos utilizaban prensas de tornillo/rosca para las aceitunas en el siglo I d.C., por lo que no parece improbable que este estilo de mordaza de banco exista desde hace mucho tiempo.
El tornillo de banco es de lo más sencillo, se utiliza un trozo de barra roscada y una tuerca para comprimir dos chuletas con la pieza de trabajo entre ellas.
Materiales:
Barra roscada M20
Tuercas M20 x 4
Arandelas M20 x 4
Madera para las chuletas – Utilicé una viga de 47mm x 255mm que me sobró de la construcción del banco.
Algo para las asas
Herramientas:
Escuadra
Regla
Broca Forsner de 20mm
Taladro
Llave de 20mm (o ajustable)
Primero marco y taladro agujeros de 20mm en la chuleta y en el delantal delantero del banco de trabajo, la profundidad se establece por 100mm de encimera más el espacio para una tuerca y una llave. Corto un hueco para una tuerca en la parte delantera del delantal para fijar la barra roscada al banco, para mí esto es >15mm de profundidad, voy un par de mm más profundo que mis tuercas M20. Aseguro la barra roscada dejando una cantidad útil que sobresale.
La placa del tornillo de banco de Moxon muestra las asas y la barra roscada una, así que girando las asas se gira la barra y se mueve la chuleta. Esto es relativamente fácil de hacer si se hace una rosca propia, dejando un trozo de madera en un extremo. Sin embargo, la fijación de un mango de acero recubierto de zinc (es húmedo en el cobertizo) es un poco más difícil, por lo que en muchos tornillos modernos baratos (como éste) la barra roscada se fija entonces las tuercas se mueven hacia arriba y hacia abajo para comprimir la chuleta. Esta es la parte trasera de mi cobertizo así que no es probable que pase por delante y se enganche en el extremo de la barra, aun así no van a estar al máximo de su extensión la mayor parte del tiempo.
Mido los mismos agujeros en la chuleta delantera y lo compruebo con la barra roscada antes de taladrar. Luego añado un par de tuercas y arandelas en la parte delantera y ya está hecho, excepto las asas.
He visto a mucha gente hacer asas de madera o de metal, todavía no he visto ninguna impresa en 3D… ¿tal vez por una buena razón? Puedo ver cómo la fuerza contra la tuerca podría hacer estallar un mango de plástico, así que voy a reforzar el mío, mi primer pensamiento fue con el metal de una lata de aerosol – esto está diseñado para resistir la expansión por lo que podría ayudar. Sin embargo, resultó ser muy, muy delgado, difícil de trabajar con él, ya que se doblaba fácilmente y era probable que me cortara los dedos, así que utilicé clips de jubilación. En el video se muestra cómo dibujé el mango en el 3D Builder, me llevó menos de cinco minutos dibujarlo, así que no es bonito, pero hasta ahora funciona bien, una vez que uno de ellos falla puedo probar otra cosa.
Descargue el pdf (pasos con imágenes) desde aquí⏬
Banco de trabajo de madera simple
D: Este es un contenido transformado y editado, el original está aquí