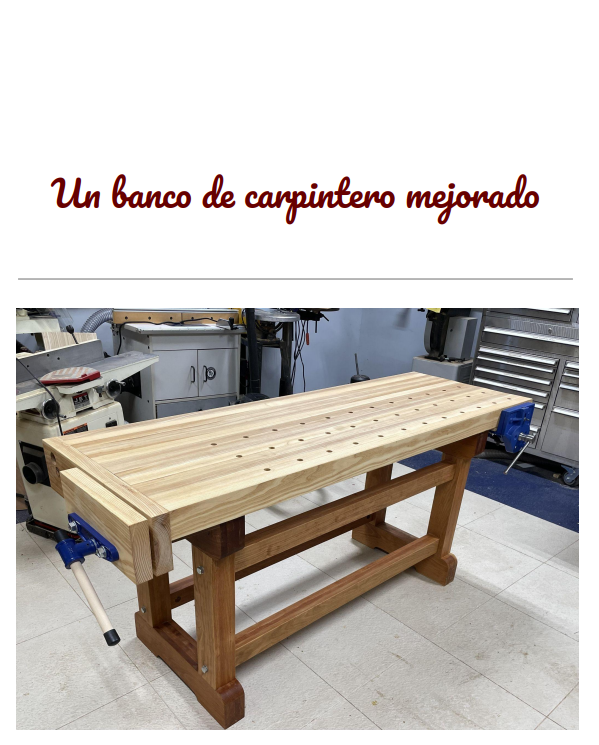
Suministros
Los suministros básicos para este proyecto incluyen
Aproximadamente 70 pies de tabla de fresno 8/4
Aproximadamente 50 pies de tabla de 4/4 de cerezo
El tornillo de banco frontal: Yost Tools F10WW Yost 10″ Front Vise
El tornillo de banco lateral: Yost M9WW Tornillo de banco para trabajar la madera de acción rápida, 9″, azul
Aproximadamente un cuarto de galón de cola Titebond III
Dos juegos de cuatro pernos de banco Highpoint de 1/2 x 6 pulgadas
Las herramientas principales que utilicé para el proyecto fueron
Tambien te recomiendo leer: Emprende con la resina epoxica y la madera creando mesas de rio . 5/5 ⭐⭐⭐⭐⭐
Sierra de mesa
Ensambladora
Cepilladora
Sierra de cinta
Lijadoras de banda y de órbita aleatoria
Taladradora
Fresadora (para las mortajas)
Abrazaderas
Taladro portátil y soporte para taladrar
También utilicé la máquina CNC para crear algunas de las plantillas y Fusion 360 para crear el diseño.
¡Sin embargo – debe este instructable como una guía de posibles diseños de banco en lugar de EL diseño definitivo que debe construir! Si trabajas con madera dimensionada, tal vez la mitad de las herramientas se vuelven innecesarias. Usando un taladro y cinceles para cortar las mortajas eliminaría la necesidad de un router. La mayoría de las piezas podrían crearse de diferentes maneras.
Paso 1: Diseño del banco
Cuando empecé a trabajar en el diseño, me fijé en los bancos que otras personas habían construido. Empecé con Etsy y algunas revistas de carpintería. También leí uno de los excelentes libros de Len Schleining y la revista Woodsmith Magazine. Veo un montón de excelentes vídeos de YouTube. Me gustó especialmente el vídeo de Rex Krueger.
Después de hacer esta investigación, empecé a hacer garabatos en mi cuaderno sobre posibles diseños. Hice algunas mediciones de algunas de las herramientas de mi taller para encontrar la altura ideal. Decidí crear algo de unas 72 pulgadas de largo con un tornillo de banco de extremo y otro lateral. La altura total es de 31 pulgadas. Opté por utilizar un diseño de trineo para las patas para que fueran resistentes. Utilicé cuatro estiradores entre los conjuntos laterales para garantizar la rigidez.
Una vez que tuve la estructura básica, utilicé Fusion 360 para hacer un diseño tridimensional. Utilicé dimensiones parametrizadas para las piezas de madera para ajustar el tamaño según fuera necesario. Me considero un novato con Fusion 360, así que encontré un excelente vídeo del sitio Around Home DIY que me ayudó a guiarme en parte de este proceso. Desafortunadamente, no pude encontrar un buen modelo 3D de los tornillos de banco Yost que estoy utilizando, así que usé esto principalmente para diseñar los subconjuntos.
La gran lección para mí con Fusion 360 fue el uso de componentes y la unión. Los proyectos anteriores que construí eran cuerpos individuales diseñados para mi impresora 3d. El trabajo en madera requiere combinar múltiples piezas y hacer múltiples copias de tablas y piezas. Me llevó un tiempo entender este proceso. Todavía soy un novato en el uso de este software, pero aquí hay algunos consejos que pueden ser útiles:
Cree sus cuerpos y luego póngalos en componentes.
Cree componentes jerárquicos – por ejemplo, mi banco está dividido en el tablero y la estructura de soporte. La estructura de soporte se dividió en cuatro tramos y dos piezas finales. Las piezas finales se construyeron a partir del soporte superior, el fondo del trineo y los dos montantes. Cada uno de los montantes se creó a partir de dos tablas exteriores y dos tablas de espiga.
Cada componente tiene su propia línea de tiempo.
Cuando se activa un componente, sólo se muestran las operaciones de ese componente en la línea de tiempo. Los componentes facilitan mucho la edición. Los bocetos, el origen, los cuerpos y las juntas también están separados.
Tenga cuidado cuando haga copias de componentes.
Cuando tiene una copia de un componente, éste hace referencia al cuerpo original del componente original. Por ejemplo, si realiza una operación de extrusión de un agujero, ese mismo agujero aparecerá en todas las copias de ese componente, ya que todas ellas hacen referencia al mismo cuerpo. En algunos casos, es posible que no desee que una característica se replique en todas las copias del componente. Para evitar que se produzcan estas modificaciones, haga una copia del cuerpo y luego convierta ese nuevo cuerpo en un nuevo componente. Dado que el nuevo componente hace referencia a un nuevo cuerpo, las operaciones sobre el original no afectarán al nuevo componente que ha creado.
La unión de componentes puede ser un poco complicada.
Cuando se utiliza el comando de unión para combinar comentarios, es necesario hacer clic en una cara, línea o punto de referencia. Sin embargo, la orientación de la unión se especifica mediante un pequeño eje ortogonal en el punto donde se hace clic. Es fácil equivocarse, sobre todo al unir una espiga con una mortaja. He cometido aproximadamente un millón de errores con esta interfaz. Fue fácil de arreglar, pero quizás un poco frustrante hasta que me familiaricé con la interfaz.
Utilizar parámetros para flexibilizar el diseño.
Puede definir un conjunto de parámetros con nombre para las medidas de su diseño. Por ejemplo, puede definir bench_top_length como 72 pulgadas. Entonces, cuando cree su mesa de trabajo, en lugar de escribir 72 pulgadas en el diseño, utilice la variable definida bench_top_length. Si es sistemático en hacer esto para todas sus medidas, puede ajustar fácilmente el tamaño del banco, y el diseño actualizará automáticamente el dibujo.
Configurar el renderizado, los dibujos y las animaciones es fácil.
Añadir colores para la madera, hacer dibujos de diseño, e incluso crear una animación para mostrar las juntas ocultas es bastante sencillo. El renderizado en 3D me ayudó a ver una vista realista de cómo quedaría el banco cuando estuviera terminado. Esto me ayudó a pensar en mis opciones de diseño. La creación de estos planos me ayudó a diseñar las juntas de algunas de las piezas. La animación del despiece me ayudó mucho a mostrar cómo se había montado todo.
Los planos del banco en PDF están enlazados a continuación. Contienen detalles sobre todas las piezas de la construcción.
Aquí están los enlaces a los archivos de Fusion 360:
El archivo de diseño principal del proyecto. (Nota: ¡la línea de tiempo está desordenada! Esto fue un experimento para mí, así que por favor sea amable).
Los dibujos que creé para el proyecto.
Una vez que estuve convencido de que el diseño funcionaría, comencé a planificar la construcción y a comprar la madera.
Paso 2: Unas palabras sobre el marcado, la medición y el corte
Siempre que creo un proyecto complejo, dedico mucho tiempo al trazado. Este proyecto se ha construido con 44 piezas de cerezo y 15 de fresno. Hay nueve formas básicas diferentes. Utilicé cuadernos, tiza, marcas de lápiz e incluso una hoja de cálculo para hacer un seguimiento de todo.
Por lo general, utilizo tiza para asignarles un número o un nombre. La tiza es fácil de quitar de las pizarras y es fácilmente visible.
Utilizo un portaminas para marcar los cortes. Suelen ser para indicar aproximadamente dónde estará el corte.
En la mayoría de los casos, confío en los topes y las plantillas para realizar la alineación.
Utilizo cuadernos y hojas de cálculo para ayudar a calcular el uso más eficiente de la madera. (Hay más discusión sobre esto en la siguiente sección).
Al hacer la disposición de las tablas cortadas en bruto, este proceso fue crítico. Marcar el número de piezas que podía obtener de cada tabla en bruto me ayudó a utilizar la madera de forma eficiente. También me ayudó a no cortar algo en el lugar equivocado – al menos en su mayoría.
Paso 3: Preparación de la madera para la tapa del banco
Para este proyecto decidí utilizar fresno para la tapa del banco y cerezo para la estructura de soporte del banco. Inicialmente, pensaba utilizar arce duro en lugar de fresno. Sin embargo, mi proveedor local no tenía suficiente madera de arce duro de 8/4 disponible, y el fresno es una hermosa madera dura y un buen sustituto para esta parte del proyecto.
Compré unos 90 pies de tabla de fresno 8/4 para este proyecto y aproximadamente 70 pies de tabla de cerezo 4/4. El coste por pie de tabla fue de unos 5 y 6 dólares por pie de tabla. El costo total de la madera en el proyecto fue de $965. A pesar del cepillado, hubo algunos residuos inevitables en el proyecto de cepillado, lijado, rasgado, recortes, etc. Todavía tengo tal vez 20 pies de tabla de material de desecho que voy a utilizar en otros proyectos.
Fijé el grosor de mi mesa de trabajo en 3 pulgadas con una longitud de 72 pulgadas. Sin embargo, la madera que encontré ya estaba cepillada en tablas con un grosor de 1,8 pulgadas. Planeé cortar las tablas en anchos de 2,5 a 3,5 pulgadas, y luego pegarlas a lo largo de sus caras cepilladas. Basándome en lo que he leído y en algunos experimentos en el taller, no tiene mucho sentido tener un banco más ancho que 30 pulgadas. Cualquier anchura mayor dificulta el acceso a las herramientas o a la pieza. Como mis tablas tenían un grosor de 1,8 pulgadas, necesité 14 piezas para que el ancho del banco fuera de 25,6 pulgadas.
Cuando compras madera de 8/4 en un almacén de madera, viene en anchos aleatorios. Las tablas de mi proyecto oscilaban entre 6 y 10,5 pulgadas. Sabía que tenía que conseguir 14 tablas de 72 pulgadas de largo y 3 pulgadas de ancho, así que utilicé una cinta métrica para determinar cuántas piezas podía obtener de cada tabla. Tuve cuidado de evitar los cuadros o nudos que pudieran interferir con la construcción. Como resultado, compré aproximadamente un 20% más de madera de la que necesitaba, sabiendo que algunos errores acabarían creando piezas más pequeñas para nuevos proyectos.
Una vez que tuve la madera en casa, cepillé uno de los bordes. A continuación, medí la anchura mínima utilizable de cada tabla. A continuación, numeré cada una de las tablas con tiza. A continuación, introduje la anchura de la tabla y el número en una hoja de cálculo. Utilizando la hoja de cálculo, experimenté con diferentes anchos para determinar el grosor máximo que podía utilizar para mi mesa de trabajo. Con estos datos, calculé cuántas tablas obtendría de mis tablones utilizando anchos de 2,5 a 3,5 pulgadas. Incluí la anchura del corte de la sierra en los cálculos. Descubrí que podía obtener 15 piezas con anchos de aproximadamente 3,1 pulgadas con la madera que compré. Como necesitaba 14 tablas para crear un banco de 25,8 pulgadas de ancho, esto me daría una tabla extra si hubiera problemas de montaje.
Utilicé mi sierra de mesa para cortar transversalmente las tablas a unas 75 pulgadas. Quería que fuera un poco más largo que la longitud final del banco para limpiar cualquier desnivel o problema que pudiera surgir en el encolado.
Dediqué algo de tiempo a afinar mi sierra de mesa para asegurarme de alinear con precisión la guía e instalé una buena hoja de corte. Utilicé tablas de plumas en los laterales y en la parte superior de las tablas. También monté una mesa de salida. Por último, ajusté la guía a unas 3,1 pulgadas, encendí el colector de polvo y empecé a cortar la madera.
Paso 4: Pegado de la mesa de trabajo
El encolado de las piezas de la mesa fue un proceso largo. No quería intentar montar todas las piezas de una sola vez, así que opté por hacer primero cuatro subconjuntos. Dos de los subconjuntos tenían 3 tablas y los otros dos tenían 4 tablas.
Pasé cada una de las tablas con la ensambladora para asegurarme de que un borde estaba completamente plano. Estaba casi plano después de ser cortado por una sierra de mesa, pero quería facilitar el proceso de acabado.
Puse dos tablas en una superficie nivelada en el suelo de mi taller a unos 5 pies de distancia. (Me aseguré de que el sistema ESTABA nivelado antes de empezar a pegar.) Escogí cada tabla para que coincidieran en grano y grosor. Las coloqué en las abrazaderas y probé el proceso de ensamblaje. Me aseguré de que la superficie recién unida estuviera orientada hacia las abrazaderas. Tras examinar la veta, apliqué cola Titebond III a las superficies cepilladas de la madera, teniendo cuidado de extender una capa uniforme por toda la superficie. Una vez aplicada la cola, alineé los extremos del conjunto y sujeté la abrazadera más cercana. A continuación, apreté la otra abrazadera.
Utilicé unas diez abrazaderas más para apretar la madera a lo largo de su superficie, (no tenía suficientes, asalté la colección de uno de mis amigos). Después de 24 horas, repetí el proceso con el siguiente subconjunto.
Una vez terminados los subconjuntos, uno de mis amigos vino con una sierra de inglete deslizante para cuadrar los extremos y asegurarse de que las longitudes de todas las piezas eran las mismas. Hubo una pieza que acabó siendo 1/8 de pulgada más larga que las demás, pero fue fácil de arreglar después con una lijadora de banda.
Como las abrazaderas de los tubos eran planas y las superficies de madera que las tocaban estaban unidas, cada subconjunto es casi perfectamente plano en una de las superficies. Pasé cada subconjunto por la cepilladora para asegurarme de que el borde opuesto era plano y paralelo a esta superficie de referencia. Pasé todas las tablas como un conjunto y luego bajé la cuchilla de la cepilladora. Seguí repitiendo hasta que todas las piezas se cortaron en toda su longitud. El grosor final de mi mesa de trabajo terminó siendo casi exactamente de tres pulgadas.
Pegué los subconjuntos de dos en dos. Una vez más, utilicé el pegamento Tightbond III, las abrazaderas de tubo niveladas y muchas abrazaderas de ayuda. Cuando empecé a unir los subconjuntos y el montaje final, me di cuenta de que había algunas deformaciones en los subconjuntos. Había algunos huecos de 1/4 de pulgada entre algunas de las tablas. Pensé en unir las superficies y luego cepillarlas. Como pude juntar las tablas con facilidad, simplemente utilicé el pegamento y las abrazaderas para arreglar el pequeño alabeo.
Una vez montadas todas las tablas, me di cuenta de que había creado algo muy grande y extremadamente pesado. Coloqué dos caballetes y le pedí a un amigo que me ayudara a levantar el tablero para poder seguir trabajando en él. Empecé por la parte inferior del banco. Utilicé un cepillo de mano y varias lijadoras eléctricas para alisar esta superficie. Como era la pieza inferior, no tenía que ser perfecta. Sin embargo, quería que se asentara firmemente sobre los soportes sin posibilidad de que se balanceara.
Pasé a trabajar en la base y las estructuras de soporte.
Paso 5: Los tableros para los soportes inferiores y superiores
Las estructuras de soporte superior e inferior del banco tienen estructuras muy similares. Me basé en el diseño de los soportes en la “unión de tres tablas de mortaja y espiga” descrita en el libro de Len Schleining. He utilizado cuatro tablas laminadas en lugar de tres, pero el diseño básico es el mismo.
La madera de la base era de cerezo para contrastar con la parte superior de fresno, más clara. Opté por utilizar madera de 4/4. Estaba preceptuada para tener un grosor de 0,8 pulgadas. Como quería una mayor resistencia, laminé cuatro de las piezas para que tuvieran un grosor de 3,2 pulgadas.
En lugar de cortar una mortaja de una pieza de madera maciza, se corta la cavidad en las tablas con una sierra y cinceles y luego se intercala entre dos tablas exteriores. De nuevo, las fotos y los dibujos deberían explicar el proceso.
Entre los dos soportes superiores y los dos fondos de los trineos, corté 32 tablas necesarias en su forma final:
Ocho tablas exteriores para los trineos.
Ocho tablas interiores para los trineos – con la misma forma exterior que la nº 1 pero con bolsillos de mortaja.
Cuatro tablas exteriores de apoyo para la parte superior.
Ocho tablas con la misma forma exterior que la #3 pero con bolsillos de mortaja.
Cuatro tablas de soporte para la parte superior son 0,8 pulgadas más largas que la #3 pero sin bolsillos de mortaja. La longitud extra de esta pieza crea una espiga que ayudará a reforzar la conexión entre el tablero y la estructura de soporte. Las 0,8 pulgadas eran arbitrarias, pero era la misma longitud que el grosor de la madera de estas piezas.
Mi primer paso fue cortar las piezas a la longitud y anchura correctas. Catorce de las piezas tenían 24 pulgadas de largo y 5,5 pulgadas de ancho. Dos piezas tenían 24 pulgadas de largo y 6,3 pulgadas de ancho.
Una vez cortadas las piezas a su anchura y longitud, creé una plantilla para los perfiles exteriores utilizando la sierra de cinta y la lijadora de banda. A continuación, hice una segunda plantilla para la base del trineo para formar el hueco entre las patas. El espacio entre los pies era de 1,5 pulgadas de profundidad y 11 pulgadas de ancho. La plantilla utilizó un redondeo de dos pulgadas en las esquinas. Después de trazar la plantilla en las piezas, corté las curvas en mi sierra de cinta.
Utilicé mi sierra de mesa con los topes adecuados para las cavidades de la mortaja para definir sus bordes. Utilicé una pieza de prueba para asegurarme de que esta mortaja se ajustaba exactamente a las tablas de espiga. A continuación, ajusté la profundidad de este corte para que fuera aproximadamente 1/4 de pulgada más profunda que la longitud de la espiga. Despues de cortar los bordes de la mortaja, piqué el material entre estos bordes. De nuevo, podría haber utilizado una sierra de cinta o una sierra de calar para hacer estos cortes, pero me pareció más rápido utilizar mi sierra de mesa para eliminar la mayor parte de la madera de desecho y eliminar las figuras restantes con un cincel y un martillo.
Como tengo un número limitado de pinzas, pegué las piezas de una en una. Utilicé Titebond III y muchas abrazaderas para asegurar un ajuste perfecto. Una vez seco el pegamento, utilicé una lijadora de banda para suavizar las curvas. Podría haber utilizado una broca de corte para suavizar los bordes o incluso cortar las piezas en mi máquina CNC. El resultado fue satisfactorio a pesar de haber tomado este atajo.
Paso 6: Los soportes verticales – Cuatro espigas de tablero
En este proyecto hay cuatro piezas de soporte vertical. Cada una de ellas está construida con cuatro tablas. Las dos tablas exteriores forman la espiga, y las dos tablas interiores crean el hombro. Las tablas exteriores miden 17 pulgadas de largo y 4 pulgadas de ancho. Las tablas interiores de la espiga miden 21 pulgadas de largo y 4 pulgadas de ancho. Hice todas las piezas con cerezo de 0,8 pulgadas de grosor.
La construcción implicó:
- Cortar las tablas a la misma longitud y anchura con mi sierra de mesa.
- Encolar las dos piezas de espiga.
- Encolar las tablas exteriores al conjunto, asegurándose de que estaban centradas con precisión en las tablas interiores.
Un problema menor en la creación de la “espiga de tres/cuatro tablas” es asegurarse de que las piezas exteriores estén alineadas con precisión. La junta de mortaja y espiga no tendrá un hombro plano si no están perfectamente alineados. He creado una plantilla sencilla (ver las fotos) para ayudar en este proceso. La idea básica es que las tablas pequeñas intercalen una tabla espaciadora de la anchura de las tablas de espiga interiores. Las piezas exteriores cortas de la plantilla se cortan transversalmente a la misma longitud en una sierra de mesa. Se desliza la plantilla sobre el extremo de las tablas de espiga y se utiliza para guiar la alineación de las espigas. Esta plantilla resolvió el problema de la alineación.
Paso 7: Montaje de los soportes
El montaje de los soportes fue sencillo. Las uniones de espiga y mortaja deben ser ajustadas, pero deben dejar suficiente espacio para el pegamento. Primero, hice una prueba de ajuste de todas las piezas para asegurarme de que todo encajaba perfectamente. A continuación, utilicé limas y cinceles para modificar poco a poco las espigas (y a veces las mortajas) para conseguir un buen ajuste. Fueron ajustes relativamente menores, pero una parte esencial del proceso de montaje. Mientras probaba el ajuste, etiqueté cada pieza. Se trataba esencialmente de modificaciones a medida, por lo que cada espiga tenía una mortaja específica y una alineación específica en esa mortaja.
Para probar el ajuste, utilicé un mazo de goma para apretar para juntar y luego separar las piezas. Una vez que estaba seguro de que el ajuste era bueno, reuní mis abrazaderas y añadí pegamento a las juntas de la mortaja. A continuación, utilicé las abrazaderas y mi mazo para asegurarme de que el hombro de las espigas de cada pieza quedaba a ras del borde de la mortaja. Tuve un momento de pánico cuando descubrí que una estaba al revés. Sin embargo, con algunos martillazos y mis abrazaderas de tubo, conseguí que funcionara. (La valiosa lección para mí fue “¡revisar siempre la alineación antes de poner el pegamento!)
Después de que el pegamento se secara, tuve que crear mortajas en las piezas verticales. Si hubiera planeado un poco más, habría hecho estas uniones ANTES del montaje. Si lo hubiera hecho, habría utilizado mi escopleadora o taladro para hacer estas cavidades. Como se trataba de una pieza ensamblada, hice una plantilla de fresado a medida utilizando mi máquina CNC. La plantilla fue hecha de madera contrachapada de 1/2 pulgada. Medí el tamaño de un cuello de router (1 pulgada) y el tamaño de mi broca de router (1/4 de pulgada). Usando la maquina CNC y un poco de matemáticas, puse la ubicación de las mortajas para que estuvieran 1.5 pulgadas por encima del hombro de la vertical y centradas en cada pieza. Incluí algunos agujeros en la plantilla tallada para ayudarme a alinear esto en el centro de la pierna vertical.
Antes de tallar la pata real, hice un corte de prueba en una pieza de desecho. Ajusté el ajuste en el diseño del CNC y luego lo volví a probar. En el segundo intento, conseguí un ajuste excelente para las espigas de las camillas. Tuve que limar los bordes de la espiga de la camilla ya que las fresadoras no pueden cortar agujeros perfectamente cuadrados, pero esto sólo me llevó unos segundos.
Una vez instaladas las mortajas, taladré algunos agujeros para montar mi soporte de taladro portátil en la plantilla de la fresadora. Primero, ajusté el soporte del taladro para centrarlo en el agujero de la mortaja. Luego, con un taladro de 1/2 pulgada, hice un agujero a través de la parte inferior del agujero de la mortaja a través de la parte exterior de la pata vertical. (Utilicé una tabla de desecho para evitar el desgarro.) Utilicé estos agujeros para los pernos de banco que sujetan las espigas de la camilla a las patas verticales.
Este es un enlace a la plantilla de la fresadora para las mortajas de las patas que creé en Easel. Es posible que necesite una cuenta de Easel para acceder a ella, por lo que he incluido los archivos SVG a continuación.
Paso 8: Las camillas
Utilicé el mismo procedimiento que para ensamblar las patas verticales para ensamblar las camillas. Como se trata de una espiga de tres tablas, creé otra plantilla para ayudar a la alineación de los hombros. Como mencioné en el paso anterior, utilicé una lima para redondear ligeramente las esquinas de la espiga. Este ajuste permitió que encajara en los agujeros de mortaja creados en las patas verticales.
Una vez pegadas las tablas, encontré algunos problemas de alineación a lo largo de la tabla. Como eran menores, utilicé una lijadora de banda para alisar estos bordes.
Paso 9: Montaje del soporte
Después de construir las dos piezas finales y las camillas, monté el soporte para sujetar el tablero. Opté por hacer este montaje con las camillas en vertical para que fuera más fácil clavar todo en su sitio. Luego bajé la segunda pieza lateral a la parte superior. Despues de hacer algunos ajustes finales, utilicé un martillo para apretar las juntas de mortaja entre las camillas y las piezas laterales. Una vez que todo estaba seguro y cuadrado, taladré los agujeros para los tornillos del banco.
Compré los pernos de banco (pernos de banco Highpoint de 1/2 x 6 pulgadas) en Woodcraft. Requieren un agujero de 1/2 de ancho y 6 pulgadas de profundidad. Como tengo cuatro camillas, necesité comprar dos juegos de estos pernos. En primer lugar, creé un bloque guía en un trozo de fresno de 2 pulgadas utilizando mi taladro. A continuación, perforé los agujeros a la profundidad requerida utilizando los agujeros preperforados en las mortajas. Utilicé una broca larga con un collarín de tope para esta operación. Mirando hacia atrás en esta operación, está claro que debería haber hecho estos agujeros ligeramente más grandes. El espacio extra hubiera ayudado con la alineación de los pernos cruzados. Sin embargo, utilicé una broca estándar de 1/2 pulgada en mi montaje.
Encontrar la posición para perforar los agujeros de los pernos cruzados fue difícil. Como estos agujeros tienen 6 pulgadas de profundidad, una pequeña desalineación de la broca puede mover la ubicación fracciones de una pulgada. Esta desalineación puede hacer que sea imposible enroscar el perno en el travesaño.
Inicialmente, coloqué la broca en el agujero y utilicé una guía láser para marcar la ubicación aproximada para perforar el agujero. Después de buscar en Google, encontré un excelente artículo de Matt Kenney con algunas plantillas que pueden ayudar a hacer esto más fácil. Utilicé su segundo diseño para hacer una plantilla para mi proyecto.
Incluso con esta plantilla, utilicé una broca Forstner 1/8 más grande que el tamaño del perno transversal. Agrandar este agujero era probablemente innecesario, pero me pareció mejor ser prudente que tener que arreglar el problema más tarde.
Una vez taladrados todos los agujeros, utilicé una carraca para apretar los pernos. Combinando la mortaja y la espiga con los pernos de banco se consigue una unión sólida y un sistema rígido. Puedo desmontar este proyecto si necesito moverlo.
Paso 10: Fijación de la parte superior
Con el soporte ensamblado y la tapa del banco montada, era el momento de conectar las dos piezas.
Trazado de los agujeros de embutición en la tapa del banco
Después de colocar el tablero del banco sobre los caballetes con la parte superior del banco hacia abajo, puse el soporte invertido sobre esta pieza. En un paso anterior, ya había alisado y aplanado la parte inferior de la bancada. Coloco cuidadosamente el soporte en su posición final. Tengo que asegurarme de que hay suficiente espacio para los tornillos de banco antes de proceder.
Se puede ver en la foto que el soporte parece estar ligeramente por encima de la mesa de trabajo porque las espigas se extienden alrededor de 0,8 pulgadas en sus mortajas. Una vez que la estructura de soporte estaba en su posición final, utilicé un lápiz para marcar la ubicación de estas espigas en la mesa de trabajo.
Después de mirar el agujero de la mortaja que iba a crear, me di cuenta de que era casi el ancho del banco. Esta anchura parecía innecesaria e incluso podría debilitar la pieza, así que decidí acortar la longitud de las espigas en las piezas de soporte en 3 pulgadas a cada lado. Utilicé una sierra de afeitar y un cincel para limpiar esta espiga. Luego ajusté mis marcas en la mesa de trabajo al tamaño de la pieza.
Para cortar los agujeros de la mortaja, creé otra plantilla en mi máquina CNC para que tuviera exactamente la longitud y la anchura adecuadas para estas piezas. Construí el patrón para acomodar un collar de fresado de una pulgada y una broca de 1/4 de pulgada. Podría haber hecho este corte con un borde recto o incluso con dos bordes rectos paralelos, pero el CNC estaba disponible y era fácil de usar para mí. Antes de usar la plantilla en la pieza, hice un corte de prueba para asegurarme de que la espiga tendría el ajuste correcto. Hice pequeños ajustes en el diseño de mi plantilla, corté una nueva pieza y el nuevo ajuste me pareció ideal.
Como la madera se expande de forma diferente perpendicular a la veta que a lo largo de la misma, tuve que prever el movimiento de la madera en estas mortajas. Basándome en las calculadoras de expansión de la madera que encontré en Internet, decidí ampliar la longitud de la mortaja en 1/4 de pulgada a cada lado. Ya que un solo perno sujetará la parte superior al chasis, esto debería dar mucho espacio para el movimiento de la madera.
Hice el fresado de la mortaja en varias pasadas. Cada pasada agrego cerca de 1/4 de pulgada de profundidad. Corté la profundidad para que fuera de 0.9 pulgadas – cerca de 0.1 pulgadas más profundo que la espiga. Cuando intenté colocar la mesa en los agujeros de la mortaja, tuve que hacer pequeños ajustes. Volví a colocar la plantilla de la mortaja y quité unos 1/16 de pulgada del borde interior de uno de los agujeros, y el soporte encajó bien en su posición.
Instalación de los tirafondos
La parte superior de la mesa se fija con tirafondos de 5/8 x 6 pulgadas que se conectan a través de la pieza de soporte en el tablero. Inicialmente, cuando estaba diseñando la pieza, había asumido que debía colocar este tirafondos en el centro del tablero y el soporte. Antes de taladrar este agujero, hice una comprobación rápida con mi tornillo de banco y descubrí que si lo desplazaba unos 5 centímetros, la instalación de esa pieza sería mucho más manejable. (Hablaré de la instalación del tornillo de banco en el siguiente paso,)
Para estos tirafondos, perforé tres agujeros concéntricos. El primero fue un agujero de 1 1/2 pulgada para hundir el tirafondos alrededor de 1/2 pulgada. El hundimiento del perno oculta la cabeza del perno, pero también ajustó la longitud efectiva del perno para que fuera ligeramente más profundo en el tablero de la mesa. El siguiente agujero era de 5/8 de pulgada de ancho, perforado a una profundidad que permitiera que la cabeza no roscada del perno encajara sin atascarse. El último agujero era un agujero piloto para el perno que iba 6 pulgadas a través de la base en la mesa. Encontré varias sugerencias sobre el tamaño del agujero piloto para un tirafondos de 5/8 pulgadas. Probé varias brocas diferentes en un trozo de madera antes de estar satisfecho con el ajuste. Decidí no publicar el tamaño de la broca aquí porque el tipo de madera parece marcar la diferencia para este diámetro. En su lugar, le animo a experimentar y encontrar el mejor ajuste para su pieza.
No perforé este agujero final hasta que volteé la mesa y la puse en su posición final. Después de invertir la pieza, instalé el tornillo y la arandela más tarde en el montaje. Antes de hacerlo, hay que ocuparse de los tornillos de banco.
Este es un enlace a la plantilla de cajeado de banco que creé en Easel. Es posible que necesites una cuenta en Inventables para acceder a ella. A continuación he incluido un archivo SVG.
Paso 11: Instalación de las mordazas – Parte I
Con el banco aún invertido y el soporte encajando a la perfección en los agujeros de la mesa, empecé a colocar los dos tornillos de banco. Como soy zurdo, coloqué el tornillo de banco final a la izquierda de mi área de trabajo. El tornillo de banco lateral está situado en el lado derecho de mi área de trabajo. Si eres diestro, estas posiciones suelen estar invertidas. (Hay una discusión sobre esto en la sección de comentarios. Pido disculpas por la confusión).
Para mi banco, he optado por comprar dos tornillos de banco diferentes:
El tornillo de banco final: Yost Tools F10WW Yost 10″ Front Vise
El tornillo de banco lateral: Yost M9WW Tornillo de banco para trabajar la madera de acción rápida, 9″, azul
El tornillo de banco final costaba unos 65 dólares. Puede alojar mordazas anchas y tiene una gran profundidad para sujetar la madera. El tornillo de banco lateral era más caro, unos 150 dólares. Tiene una palanca de ajuste rápido que facilita el bloqueo de la madera en su lugar.
La instalación del tornillo de banco lateral fue sencilla. En primer lugar, añadí una tabla espaciadora para bajar las mordazas del tornillo de banco aproximadamente 1/4 de pulgada por debajo de la superficie del banco. En esta etapa, sólo probé el ajuste. No perforé los agujeros ni coloqué la tabla espaciadora hasta que la mesa estuvo en posición vertical.
Para el tornillo de banco final, desatornillé y retiré el conjunto roscado y coloqué el carro en su lugar. Como necesitaba hacer agujeros a través del soporte del extremo para este tornillo de banco, hice algunas mediciones cuidadosas y creé una plantilla de perforación en Fusion 360. En primer lugar, dibujé un sencillo dibujo bidimensional para mostrar la ubicación de la rosca y las varillas de soporte. A continuación, coloqué un espaciador de 3/4 de pulgada por debajo del tablero de la mesa para bajar el tornillo de banco. Este ajuste acercó los agujeros necesarios al centro de las estructuras de soporte.
La creación de la plantilla fue un poco enloquecedora. Encontre una guia de maquina, tome medidas cuidadosamente, dibuje la plantilla, y luego la imprimi. Cuando la imprimí, al final era del tamaño incorrecto. Volví a tomar las medidas e imprimí una nueva versión con el mismo resultado. Pasé por media docena de iteraciones antes de darme cuenta de que la configuración por defecto de mi impresora reproducía los dibujos a un 97% de su tamaño real. Consejo de experto: asegúrate de imprimir a un tamaño del 100% cuando crees dibujos a escala.
Taladrar los agujeros a través del soporte fue sencillo. Utilicé brocas de aproximadamente 1/4 de pulgada más grandes que el agujero del tornillo y las barras de soporte. Utilicé brocas de pala y mi guía de perforación portátil. También sujeté una tabla en la parte inferior para evitar que se astillara.
Paso 12: Atornillar la mesa al soporte
Normalmente no dedicaría un paso completo a describir la instalación de dos tornillos. Sin embargo, este paso resultó ser más difícil de lo esperado.
El problema fundamental es el peso de la pieza. La estructura de soporte pesa alrededor de 50 libras. La mesa de trabajo pesa más de 100 libras.
Un amigo me ayudó a dar la vuelta a la encimera y a colocarla en su sitio. Asegúrate de hacer esto si construyes un proyecto como este. No te hagas daño. Pide ayuda a un amigo.
Paso 13: Aplanar la tapa del banco
Tal vez la mejor manera de hacer un banco perfectamente plana es utilizar un trineo router. Hay varios buenos Instructables sobre cómo aplanar las tablas usando una router. Le animo a mirar estos si usted está creando un banco.
Mi enfoque fue un poco más simple. En primer lugar, me aseguré de que cada tabla era perfectamente plana usando un carpintero. A continuación, utilicé dos tablas de referencia planas y paralelas para crear 3-4 conjuntos de tablas. Finalmente, utilicé dos abrazaderas de tubo que estaban planas y niveladas para ensamblar estos conjuntos de 3-4 tablas. Las abrazaderas aseguran que las piezas estén en el mismo plano, incluso si una tabla individual está ligeramente fuera de lugar.
El resultado tras el encolado fue casi satisfactorio. Sin embargo, había algunos lugares donde una tabla estaba fuera de lugar por alrededor de 1/16 de pulgada. Eran cambios bruscos en la superficie que había que arreglar.
Usando un cepillo de mano y una lijadora de banda, trabajé lentamente a través de la superficie para eliminar estos puntos altos. Intenté trabajar toda la longitud de la mesa por igual, lijando siempre a favor de la veta. Utilicé repetidamente una regla para comprobar la planicidad del tablero. Ajusté el lijado y el cepillado para reducir los puntos altos y evitar las partes bajas de la superficie de la mesa. Pasé a una lijadora de órbita aleatoria con papel de grano 60 para las etapas finales.
Lijar y aplanar la parte superior me llevó horas. Utilicé un aspirador de taller y mi sistema de filtración de aire para ayudarme en este proceso, pero fue un trabajo tedioso y cuidadoso.
Al final del proceso, la mesa estaba extremadamente lisa y plana por debajo de 1/16 de pulgada. La mayoría de los lugares son mejores que 1/32 de pulgada. La pregunta obvia es: “¿Es esto suficientemente bueno?” Desafortunadamente, no hay una respuesta simple a esta pregunta. Aprenderé más sobre cómo funciona en la práctica a medida que utilice el banco. Si necesito mejorar la planicidad, montaré un trineo de fresado y aplanaré el banco adecuadamente. Por ahora, no creo que sea crítico tenerlo mejor que sus especificaciones actuales.
La lección importante fue esta: Si no es lo suficientemente bueno, siempre puedo volver atrás y arreglarlo. El banco puede modificarse y evolucionar a medida que crezcan mis necesidades. No crees trabajo innecesario sólo porque crees que PODRÍA ser necesario.
Paso 14: Instalación de las mordazas
Para instalar el tornillo de banco lateral, atornillé la placa espaciadora en la parte inferior de la mesa de trabajo utilizando dos tornillos #12 x 2 pulgadas. A continuación, coloqué el tornillo de banco en su posición final utilizando abrazaderas y marqué la ubicación de los tirafondos. El tornillo de banco Yost M9WW tiene dos ranuras en forma de “U” para los tirafondos que pueden ayudar a mantener temporalmente el tornillo en su lugar mientras se hunden los tornillos restantes. Primero instalé esos tornillos, volví a sujetar el tornillo de banco a la mesa y luego instalé los dos últimos tornillos.
Esta operación habría sido más fácil si la mesa de trabajo hubiera estado al revés. Aunque me preocupaba el peso extra, debería haber instalado las placas espaciadoras y avellanado los agujeros de los tirafondos antes de instalar el tablero. En última instancia, voy a añadir almohadillas de mandíbula a este tornillo de banco. Todavía estoy considerando la posibilidad de colocar mordazas de madera y un simple acolchado.
El primer paso es montar la base del tornillo de banco en su ubicación final. Atornillé la pieza espaciadora en su posición con tornillos del nº 12 x 2 pulgadas. A continuación, coloqué la base del tornillo de banco en su posición aproximada utilizando una abrazadera. A continuación, utilicé una clavija de 1 pulgada para asegurarme de que el tornillo de banco y las varillas de soporte para el tornillo de banco pasaran por los agujeros que perforé en el soporte vertical. Cuando estuve satisfecho con el ajuste, instalé los tirafondos para sujetar la base del tornillo de banco en su sitio. Después de instalar el primer tornillo, volví a comprobar la alineación con el resto del tornillo de banco. El objetivo era asegurarme de que el tornillo y las barras de soporte encajaban antes de instalar más tornillos. Afortunadamente, todo funcionó bien. Finalmente, retiré el conjunto de tornillos del tornillo de banco e instalé los tirafondos restantes.
La instalación del tornillo de banco en el banco fue más compleja. Hay que crear las mordazas para el sistema, y la mordaza trasera tiene que estar montada de forma segura en la mesa de trabajo. Opté por añadir un trozo de fresno de 1,8 pulgadas de grosor al extremo del banco.
En primer lugar, corté la pieza del mismo ancho que el banco. Luego, sujeté temporalmente la pieza al extremo de la mesa de trabajo. A continuación, marqué los lugares aproximados para los tirafondos que conectarán la pieza al extremo y los agujeros necesarios para el tornillo de banco y las varillas de soporte.
Usando mi prensa de taladro, avellané tres agujeros con una broca Forstner de 1,5 pulgadas a una profundidad de aproximadamente 3/4 de pulgada. Uno de estos tres agujeros estaba cerca del centro de la mesa. Los otros dos agujeros estaban a unas 10 pulgadas del centro a cada lado. Desplazé todos los agujeros 1,5 pulgadas desde la parte superior de la pieza. En el centro de los agujeros de 1,5 pulgadas, perforé agujeros de 5/8 pulgadas para los tirafondos. Para permitir el movimiento de la madera, alargue los dos agujeros exteriores.
Usando la plantilla que creé para taladrar los agujeros a través de la pieza de soporte para el tornillo de banco, marqué la ubicación de los agujeros para los tornillos del tornillo de banco y las barras de soporte. Al igual que antes, volví a comprobar estas posiciones utilizando una clavija que pasaba por la base del tornillo de banco.
Perforé el agujero para el tornillo de banco utilizando una broca Forstner a través de la pieza. Las varillas de soporte requieren dos agujeros concéntricos: uno lo suficientemente grande para las varillas y un segundo agujero de 1,25 pulgadas para sujetar los collares del tornillo de banco. Estos pequeños collares metálicos se atornillan en su lugar y actúan para dar rigidez a la estructura de soporte del tornillo de banco. Utilicé tres tornillos (#14 x 1-pulgada) para cada uno de estos collares para asegurarlos.
Después de comprobar el ajuste, avellané e instalé la pieza utilizando tirafondos de 5/8 x 5 pulgadas. Usar algo tan pesado era probablemente innecesario, pero aseguraba un ajuste sólido. Además, los agujeros del taladro atraviesan el extremo de la mesa de trabajo, así que pensé que usar tornillos más grandes aseguraría que el ajuste fuera estable. Primero instalé el tornillo central y luego los dos tornillos exteriores.
Para crear la mordaza, utilicé otra pieza de fresno de 1,8 pulgadas. Basado en mi ubicación de instalación, el ancho de la mandíbula era de 15 pulgadas. Utilizando la plantilla de perforación, marqué la ubicación de los agujeros y utilicé mi prensa de perforación. La mordaza se fijó con tornillos del nº 14 x 1 1/4 de pulgada.
Una vez instalada la mordaza, tuve que hacer un pequeño ajuste. La mordaza tenía una ligera flexión cuando la apreté sobre un trozo de madera. Esta flexión hace que las superficies delantera y trasera del tornillo de banco no queden paralelas.
El manual de Yost sugería que se redujera ligeramente la parte delantera del tornillo de banco para solucionar la flexión de la mordaza. Como mi mordaza era algo más profunda que el ejemplo del manual, utilicé un espaciador de 1/8 de pulgada y pasé la mordaza por mi cepillo para crear esta conicidad. Funcionó muy bien. Las mordazas quedaron paralelas al apretarlas.
Algunas reflexiones finales:
La instalación de este tornillo de banco fue un proyecto complejo en sí mismo. Hay muchos recursos buenos que puedes usar para ayudarte, incluyendo
Vídeo en Youtube de Timothy DC
Vídeo en Youtube de Gerald Etto
Vídeo en Youtube de Anthony Scolaro
Instructable por Around Home
Instructable por djpolymath
Instructable de Dimensions Woodwork
Paso 15: Añadir perros de banco
Una vez instalados los tornillos de banco, era el momento de taladrar los agujeros para los perros de banco. Dediqué algún tiempo a trazar la ubicación de los posibles agujeros. Es útil tener en cuenta que no hay una manera correcta o incorrecta de elegir la ubicación de los agujeros. Sin embargo, ayuda a tener en cuenta algunas consideraciones de diseño. Estas fueron mis limitaciones de diseño:
- Las posiciones de los agujeros deben permitir sujetar cualquier longitud de pieza de madera utilizando el tornillo de banco de extremo o el tornillo de banco lateral.
- Las piezas más cortas (menos de 24 pulgadas) pueden sujetarse con el tornillo de banco lateral.
- Las piezas más largas (de 24 pulgadas a aproximadamente 72 pulgadas) pueden sujetarse con el tornillo de banco de extremo.
- Los tornillos de banco deben permitir una sujeción sencilla, ya sea a través de orificios dobles en los bordes de la tabla o de orificios centrales.
- El espacio entre los agujeros debe ser lo suficientemente pequeño como para ajustar el tornillo de banco a la madera con relativa rapidez. (No quería que el espaciado fuera demasiado grande).
- El banco debe tener el mínimo número de agujeros necesarios.
- El espaciado de los agujeros debe ser preciso para permitir que alguna futura plantilla teórica pueda utilizar múltiples agujeros si es necesario.
- La separación de los agujeros debe ser adecuada para las sujeciones y otros equipos de sujeción además de los tornillos de banco.
Basándome en estas consideraciones, decidí hacer tres filas. Centré una fila en el tornillo de banco del extremo. Centré las otras dos filas a ambos lados del centro. También quería que los perros del banco se alinearan con el tornillo de banco lateral. Por lo tanto, lo configuré de manera que dos agujeros estuvieran situados simétricamente a cada lado del centro de esta posición.
El espacio de los agujeros es de 5 pulgadas. Este espacio era aproximadamente la mitad de la profundidad de los tornillos de banco que utilicé. Me pareció que permitiría ajustar fácilmente las piezas de madera de diferentes tamaños.
Para ayudarme con la tarea de taladrar los agujeros, creé una plantilla utilizando mi máquina CNC con seis agujeros. Cada uno de los agujeros era del tamaño de mis perros de banco – 3/4 de pulgada. El espacio entre los centros de los agujeros era exactamente de 5 pulgadas. Atornillé la guía de mi taladro para alinear la broca de pala de 3/4 de pulgada para que encajara en uno de los agujeros centrales. Fijé la distancia entre el borde de la plantilla y el centro de la broca a 7,5 pulgadas. Podría haber hecho fácilmente esta plantilla en una prensa de taladro. Sin embargo, soy así de perezoso. Debo notar que usar el MDF de 1/2 pulgada para la plantilla fue probablemente un error. El orificio para la broca de pala se agrandó lentamente a medida que perforaba los agujeros. Lo hubiera construido de 3/4 de madera contrachapada si lo hiciera de nuevo.
El objetivo de la plantilla era asegurarse de que todos los agujeros estuvieran exactamente a 5 pulgadas de distancia. Como estaba considerando hacer algunas plantillas para perros de banco múltiples, el espaciado exacto ayudará con su construcción. Los agujeros adicionales de la plantilla eran para alinearlos con los agujeros que ya había perforado. Luego, con unos trozos de tacos de 3/4 de pulgada, se puede fijar la pieza para seguir el patrón.
Alineé el borde de la plantilla con el borde del banco para la fila central de agujeros. Después de taladrar el primer agujero, moví la plantilla y utilicé un taco para fijarla en su sitio. Mantuve el borde de la plantilla plano contra el borde del banco. Despues de trabajar hacia abajo a traves de las filas, use los otros agujeros para alinear los agujeros de perforacion para las dos filas exteriores.
Al taladrar los agujeros (y al hacer el trazado), tuve cuidado de observar cuando podía chocar con el carro de la mesa o la estructura de soporte. Los otros agujeros de la mesa pasan a través de todo el grosor de la mesa. Estos agujeros ayudarán a que el serrín fluya en lugar de acumularse en el fondo de los agujeros.
Taladrar los agujeros fue un proceso tedioso. Hacer agujeros de 3/4 de pulgada a través de 3 pulgadas de fresno lleva mucho tiempo. Utilicé una aspiradora para limpiar el polvo periódicamente. Además, tuve que cambiar las baterías de mi taladro cada cinco agujeros. Usar un taladro con cable hubiera sido lo más inteligente.
Nota: Los agujeros de los perros de banco en el tornillo de banco no han sido perforados todavía en estas fotos. Me fui de vacaciones antes de terminar este paso. Sin embargo, tendrán el mismo espacio que los otros agujeros.
Aquí hay un enlace a la plantilla de perforación de agujeros de perro de banco en Inventables.. Es posible que necesite una cuenta de Easel para acceder a este archivo. El archivo SVG se adjunta a continuación.
Paso 16: Acabado del banco
Lijé la parte superior hasta el nivel de grano 220 utilizando una lijadora de órbita aleatoria para terminar el banco. Después de quitar el polvo con un paño, usé aceite danés para sellar y terminar la parte superior. Este proyecto era la primera vez que utilizaba este acabado. Se inunda la superficie con el aceite utilizando un cepillo o un paño. Se mantiene la superficie húmeda durante unos 30 minutos añadiendo periódicamente más acabado. Al final de ese tiempo, se limpia el exceso y se deja secar durante 24 horas. Los acabados al aceite no se agrietan y son fáciles de refrescar si es necesario. Cuando tengo que volver a revestir mi banco, puedo aplicar el aceite para igualar el acabado anterior. El aceite también ofrece cierta protección contra las manchas, y sin duda resalta los colores y las vetas de la madera.
Cuando construí este banco, terminé la estructura de soporte antes de colocar el tablero. El acabado es más fácil antes de fijar la estructura de soporte e invertirla.
Aún quedan muchas cosas por hacer:
Primero, necesito perforar los agujeros para los perros del banco en el tornillo de banco lateral.
Tengo que acolchar el tornillo de banco lateral con madera o quizás con cuero.
Puede que instale algunas estanterías y almacenamiento. En un principio pensé que sería fundamental instalar estanterías e incluso cajones para guardar las herramientas. Sin embargo, me gusta el aspecto actual del banco, así que he decidido posponer este paso por ahora.
Puede que instale una regleta oculta en la parte trasera del banco para las herramientas de mano.
Tengo que pensar en más plantillas. Tengo algunos pernos de banco y sujeciones, pero sospecho que surgirán otras necesidades a medida que vaya conociendo esta nueva herramienta.
El coste total de este banco fue elevado: unos 1.100 dólares, incluyendo la madera, los tornillos de banco, el acabado, etc. Podría haber utilizado madera más barata, pero me gusta el aspecto final de la pieza. Tardé unos cuatro meses en construirlo, sobre todo en sesiones de 2-3 horas una vez a la semana.
A pesar del coste y el tiempo, este banco será la herramienta más utilizada en mi taller. He disfrutado haciéndolo. Espero que mis ensayos y errores os aporten conocimientos prácticos que os ayuden en futuros proyectos.
Muy importante!!
Descargue el pdf (pasos con imágenes) desde aquí⏬
Un banco de carpintero mejorado
D: Este es un contenido transformado y editado, el original está aquí